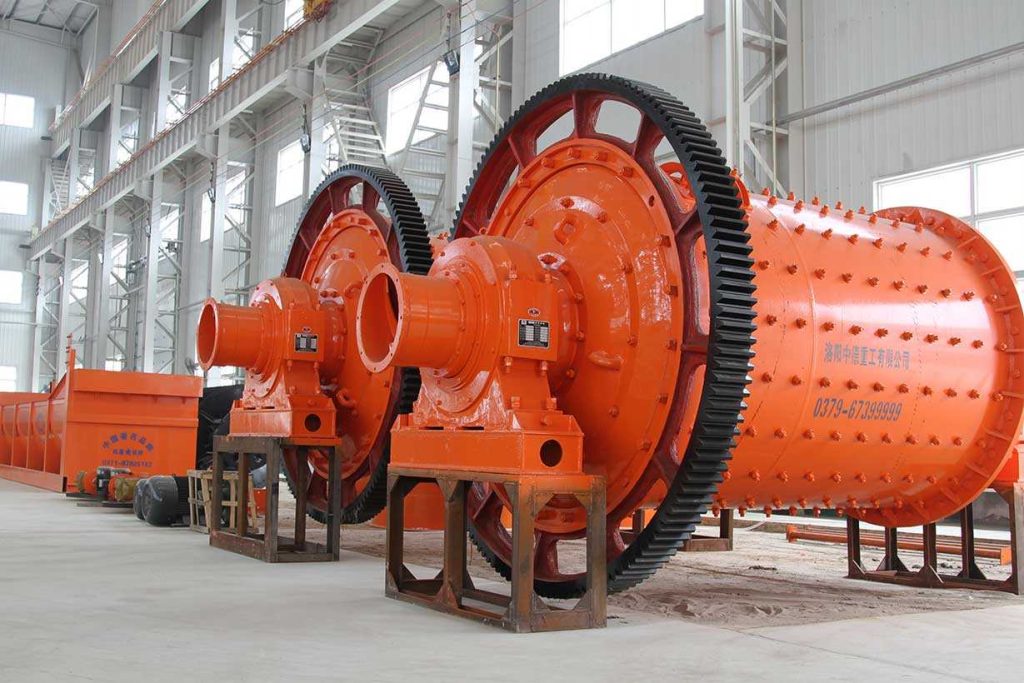
Wear-resistant liners are a critical component in the operation of mining equipment. They directly impact the equipment’s performance, lifespan, and maintenance costs. Selecting the appropriate liners and adopting proper maintenance practices can effectively extend the equipment’s service life, enhance productivity, and reduce operational costs.
I. The Primary Functions of Wear-Resistant Liners
During the handling of materials such as ore and coal, mining equipment is subject to intense wear and impact due to the materials’ high hardness and impact forces. The main functions of wear-resistant liners include:
- Protecting Equipment Bodies: Preventing damage to the equipment body caused by prolonged wear.
- Extending Service Life: Reducing the frequency of replacements and lowering maintenance costs.
- Improving Operational Efficiency: Minimizing performance degradation due to wear.
II. Selection Criteria for Wear-Resistant Liners
When choosing wear-resistant liners, factors such as equipment type, working environment, and material characteristics must be considered. Key selection criteria include:
- Wear Resistance: The liner material must have high hardness and wear resistance.
- Impact Resistance: In high-impact environments, the material should have sufficient toughness to prevent cracking.
- Corrosion Resistance: For equipment handling acidic or alkaline materials, the material must exhibit excellent anti-corrosion properties.
- Temperature Range: The material must maintain stable performance in high or low-temperature environments.
- Cost-Effectiveness: Consider both initial investment and operational costs comprehensively.
III. Advantages and Disadvantages of Common Liner Materials
Material | Advantages | Disadvantages |
High-Manganese Steel | High hardness and toughness; suitable for high-impact environments | Poor corrosion resistance, high noise levels, safety risks during maintenance |
Ceramic Materials | Extremely high hardness and excellent wear resistance | High cost, high noise, and expensive maintenance |
Polyurethane | Excellent wear resistance and elasticity; noise reduction; corrosion-resistant; lightweight and easy to maintain | High initial cost; unsuitable for high-temperature environments |
Rubber Composites | Good impact resistance and vibration absorption; lightweight | Poor low-temperature performance, lower wear resistance, shorter lifespan |
Wear-Resistant Cast Iron | High hardness and corrosion resistance; suitable for static components | Lower wear resistance; safety risks during maintenance |
IV. Maintenance Guidelines for Wear-Resistant Liners
- Regular Inspections: Establish regular inspection schedules to identify and repair or replace severely worn components promptly.
- Proper Installation: Ensure liners fit tightly against the equipment surface to avoid additional wear caused by looseness.
- Optimal Equipment Operation: Control material flow rates and drop heights to reduce excessive impact.
- Avoid Overloading: Prevent equipment from operating under excessive loads.
Kubis tech Ltd has been dedicated to polyurethane applications for many years. If you have any questions during the purchasing process or need professional advice, feel free to contact us. We are committed to providing the highest quality wear-resistant liners and the most professional services to help you reduce operating costs, enhance equipment stability, and improve production efficiency, contributing to your cost reduction and efficiency goals. Pls click here to find out more product on my website.