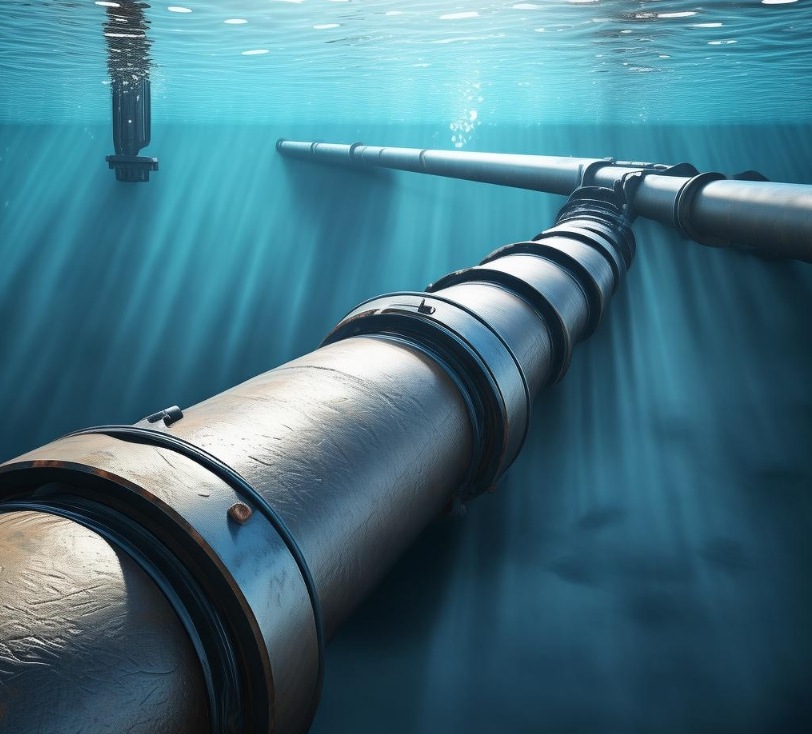
Choosing the appropriate seal for your equipment is a critical decision that requires careful consideration of multiple factors to ensure optimal performance and longevity. Here are some key factors to consider when selecting seals:
Equipment Specifications
- Dimensional requirements: Ensure the seal's dimensions, including diameter, width, and cross-sectional shape, accurately match the equipment's housing and shaft.
- Material compatibility: The seal material must be compatible with the equipment's construction materials to prevent chemical reactions or galvanic corrosion.
Operating Environment
- Temperature range: The seal must be able to withstand the operating temperature extremes without losing its sealing properties.
- Pressure: The seal must be designed to handle the anticipated pressure differential across the sealing interface.
- Media compatibility: The seal material must be chemically resistant to the fluids or gases it will come into contact with.
- Contaminants: Consider the presence of abrasive particles, contaminants, or corrosive substances that could affect seal life.
Motion Type
- Static or dynamic: Determine if the seal will be used in a static or dynamic application. Dynamic seals are subjected to relative motion, while static seals are used in stationary joints.
- Speed: The rotational speed of the shaft or other moving component will influence the seal's design and material selection.
Load and Pressure
- Axial and radial loads: Consider the axial and radial forces acting on the seal, as these will affect its design and material.
- Pressure fluctuations: If the pressure in the system fluctuates, the seal must be able to accommodate these changes without leaking.
Installation and Maintenance
- Ease of installation: The seal should be easy to install and align, minimizing downtime.
- Maintenance requirements: Consider the frequency of inspections and replacements, as well as the availability of spare parts.
Material Selection
- Chemical resistance: The seal material must be resistant to the chemicals it will come into contact with.
- Wear resistance: For applications involving abrasive particles, a wear-resistant material is essential.
- Temperature resistance: The seal must be able to withstand the operating temperature range.
Brand and Quality
- Reputable manufacturers: Choose seals from reputable manufacturers with a proven track record of quality and reliability.
- Industry standards: Ensure the seal meets relevant industry standards and certifications.
Cost-effectiveness
- Initial cost: Consider the upfront cost of the seal.
- Lifetime cost: Factor in the cost of installation, maintenance, and potential replacements over the seal's lifetime.
Need Assistance?
If you're unsure about which seal is best suited for your specific application, our technical experts at Kubis tech Ltd. are here to help. Please provide us with detailed information about your equipment, operating conditions, and the fluids or gases being sealed. We will be happy to recommend the most suitable seal for your needs.