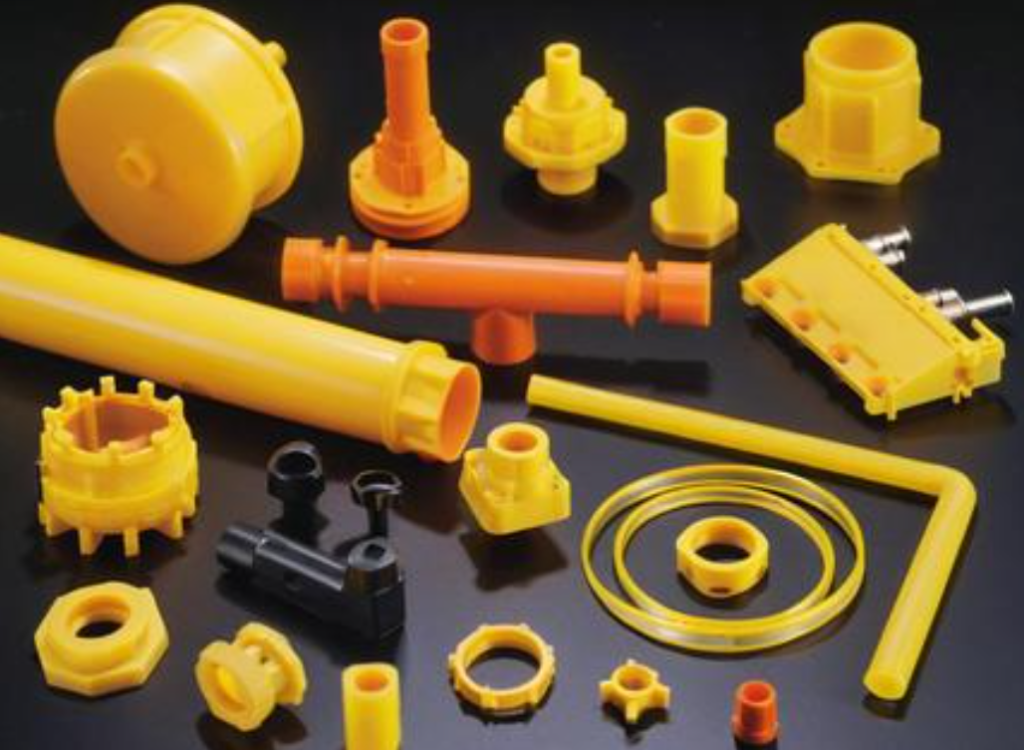
Polyurethane elastomers, renowned for their high strength, elasticity, and abrasion resistance, are classified based on processing methods and molecular structure. These versatile materials find extensive applications in footwear, automotive components, medical devices, and cable protection.
Classification by Processing Method:
- Cast Polyurethane Elastomers (CPU): Formed by pouring a mixture of raw materials into a mold, resulting in a thermoset network structure. CPUs offer excellent abrasion resistance and toughness, making them suitable for high-strength components.
- Thermoplastic Polyurethane Elastomers (TPU): These materials can be softened by heating and harden upon cooling, providing excellent processability and physical properties. TPUs account for approximately 25% of the total polyurethane elastomer market.
- Moulded Polyurethane Elastomers (MPU): As the earliest type of polyurethane elastomer, MPUs are processed using conventional rubber processing equipment. They are produced by synthesizing a stable solid gum, which is then further processed.
Classification by Molecular Structure:
- By Soft Segment:
- Polyester-based: Containing ester groups, they typically offer excellent abrasion resistance and strength.
- Polyether-based: Containing ether groups, they generally exhibit better flexibility and low-temperature performance.
- Butadiene-based: Containing butadiene groups, they are suitable for specific applications.
- By Hard Segment:
- Urethane-based: Obtained from diol chain extenders, they provide higher rigidity.
- Urethane-urea-based: Obtained from diamine chain extenders, they typically offer better chemical resistance.
Outstanding Properties of Polyurethane Elastomers:
- High strength and elasticity with a wide hardness range (Shore A10 to D85).
- Excellent abrasion resistance, tear resistance, cut resistance, and ozone resistance.
- Versatile processing capabilities, allowing for the production of foams, coatings, adhesives, and more.
Applications of Polyurethane Elastomers:
- Footwear: Used in athletic shoes, casual shoes, and more to enhance comfort and durability.
- Automotive components: Such as bumpers and door skins.
- Medical devices: As a safe and non-toxic alternative to PVC.
- Cable protection: Providing tear-resistant and abrasion-resistant protective layers.